6月11日8时,广东交通集团发布消息,世界最长最宽钢壳混凝土沉管隧道——深中通道海底隧道最终接头顺利推出,贯通测量结果表明,实现了与东侧E24管节精准对接。目前,深中通道海底隧道已实现合龙,将开展最终接头后焊段施工等,力争11月实现隧道贯通;桥梁工程已经合龙,人工岛工程按计划推进,路面、机电、房建交安和管内工程已经全面展开,正向2024年项目建成通车奋力冲刺。
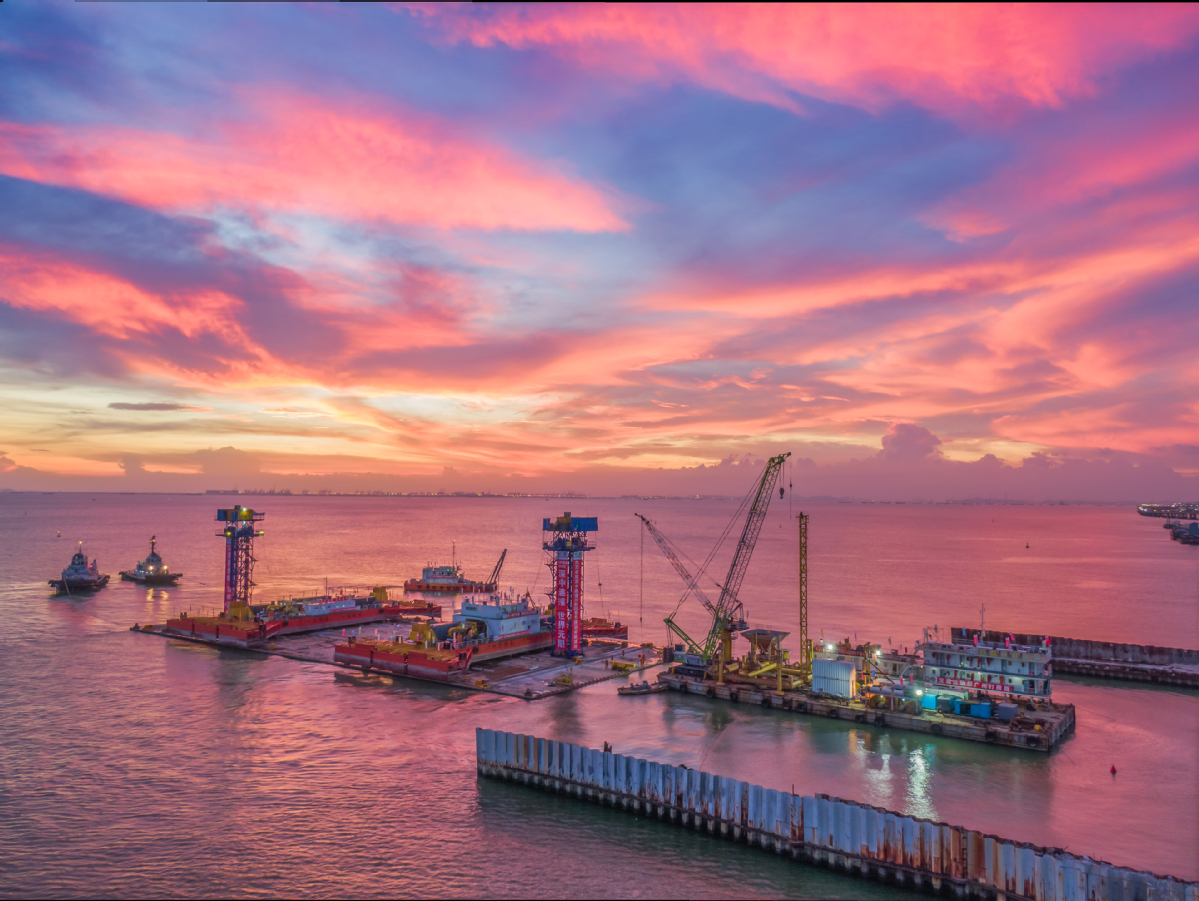
深中通道全长24公里,集“桥、岛、隧、水下互通”于一体。其中,海底隧道长约6.8公里,包含沉管段约5公里,由32个管节及1个最终接头组成。此前,深中通道海底隧道已由东西两侧往中间依次沉放对接了31个管节。6月8日开始最后一个管节(E23)及最终接头的整体浮运安装,至今日完成最终接头推出对接,共用时近70个小时,一举实现关键控制性工程突破。
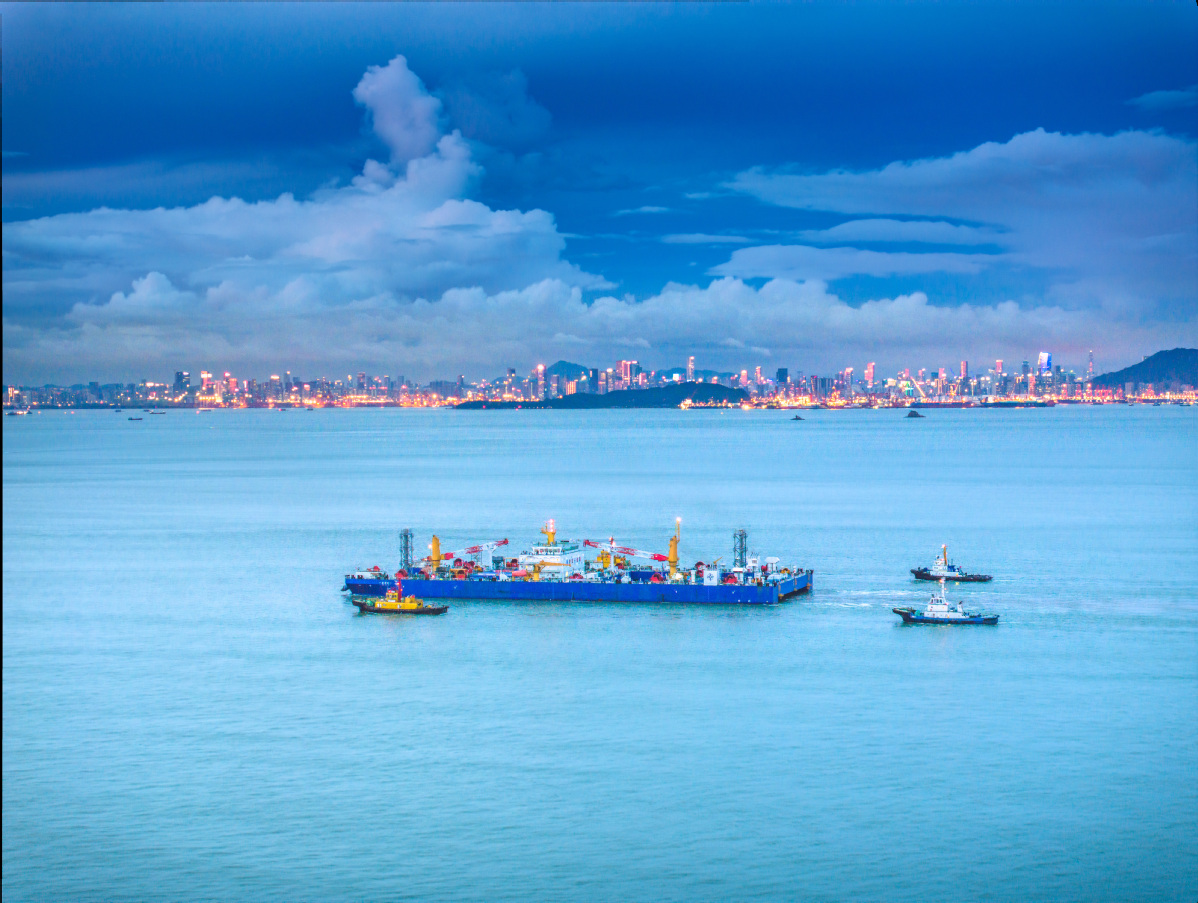
据了解,海底沉管隧道工程共分为三大关键技术:基础处理、管节浮运安装及接头处理。其中,基础处理包括基槽开挖、软基处理及基床整平。基础处理的要求极高,海底20-40米深处基槽开挖精度、碎石整平精度均要求达到亚米级,堪称“海底绣花”。深中通道项目采用的复合地基处理新技术,软土地基沉降控制在48毫米以内,达到国际领先水平。海底隧道长约6.8公里,总用钢量约32万吨。其中一个标准管节长165米、宽46米、高10.6米,立起来就是一幢55层的大楼。平均每节沉管的用钢量约1万吨,焊缝长度超过270公里。
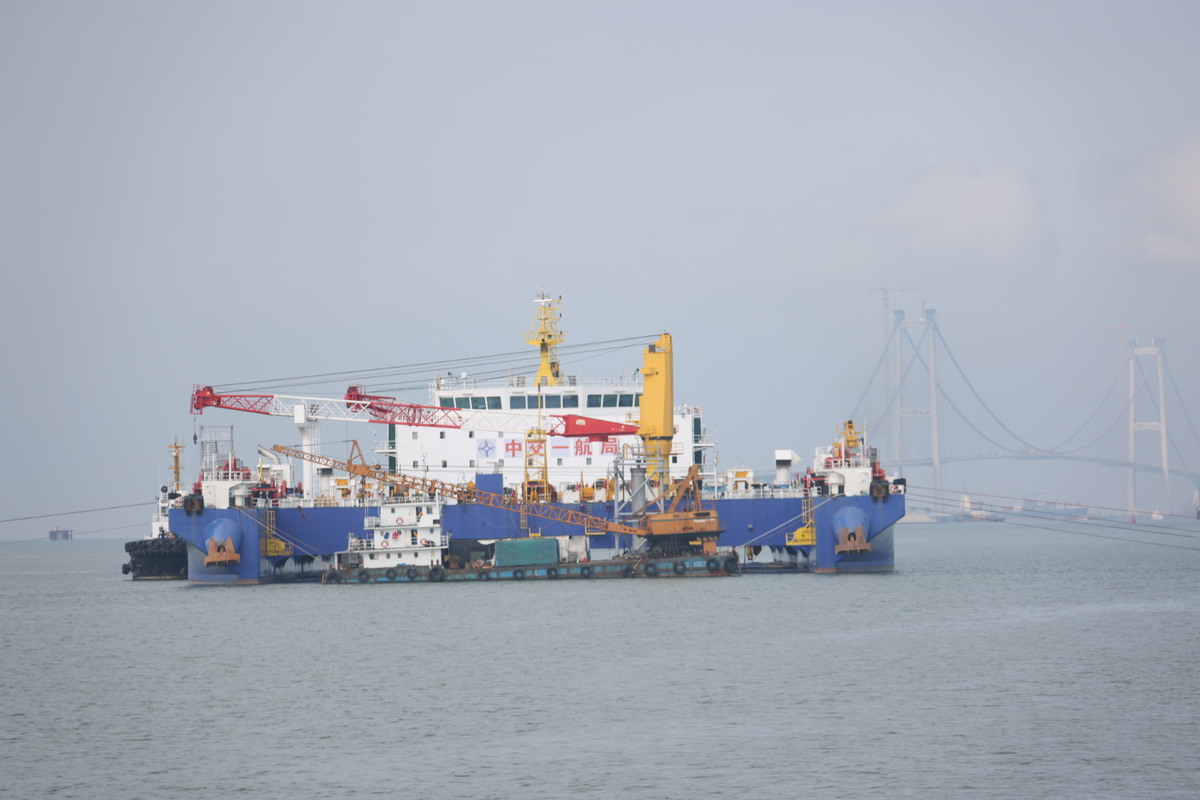
钢壳制造完成后,由中交四航局桂山岛沉管预制厂负责23个管节的预制,保利长大黄埔文冲龙穴岛沉管预制厂负责9个管节的预制,两处均采用智能浇筑系统进行自密实混凝土的浇筑。中交四航局深中通道项目部生产副经理罗兵介绍,经过三年多的平行研究,开展了上百组模型试验,项目研制出了高稳健、高流动性的自密实混凝土,还研发出了具备自动寻孔、自动行走、自动控制浇筑速度的智能浇筑装备及系统,极大提升了浇筑质量和速度。据了解,深中通道钢壳沉管管节共浇筑了近90万立方米的自密实混凝土,检测表明,混凝土填充密实性达到国际领先水平。
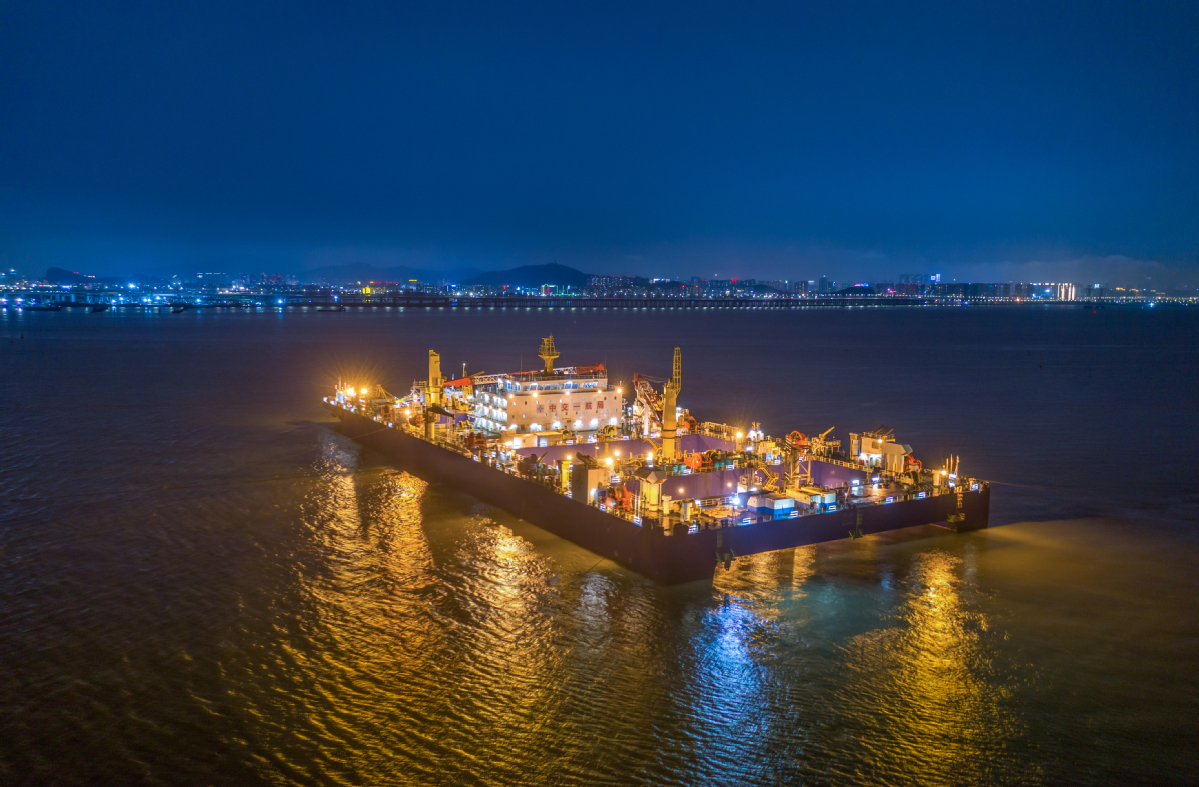
6月11日,深中通道最终接头实现了与E24管节的精准对接。据悉,深中通道沉管隧道采用的整体预制水下管内推出式最终接头,是世界首创的全新结构装置,将最终接头与最后一节沉管(E23)一同制造,推出段放置在管节对接端的扩大端内,与最后一节沉管一并浮运沉放,待最后管节标准段与已安装管节完成对接并确认姿态合适后,推出段就像一个巨型的抽屉内盒,利用千斤顶将推出段(抽屉)从一侧推出,与E24管节的端钢壳完成对接。
深中通道管理中心总工程师宋神友介绍,这种接头具有安全性好、施工快速、不需要大型装备、经济性好等优点。创新采用这种新接头形式的出发点和目的,是希望在外海沉管隧道建造中,形成更加安全、更加高效、更加精准的对接,同时在世界沉管隧道施工领域中实现新的突破,扩大我国在该领域的领先优势。
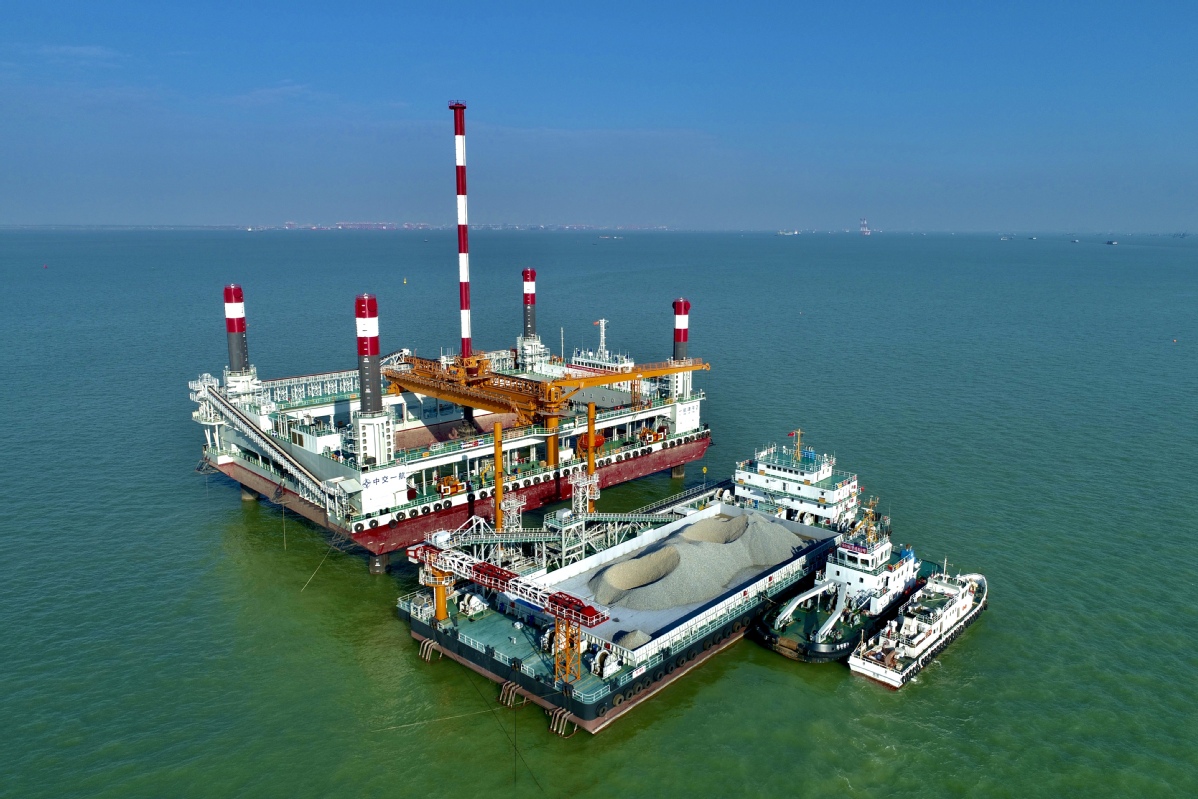
为了实现沉管超长距离的安全浮运,并进一步提升沉管安装的精度,历经三年的平行研究,深中通道建设团队研发了世界首艘且唯一一艘沉管浮运安装一体船“一航津安1”,它是当前世界上安装能力最大、沉放精度最高、施工作业最高效、性能最先进的沉管运输安装专用船舶,可满足8万吨级沉管50公里超长距离安全浮运安装作业,减少伶仃航道占用时间80%以上,减少临时航道挖泥70%以上,沉管浮运安装效率较传统工艺提升一倍以上。沉管浮运安装一体船系统性革新了世界沉管浮运安装工艺,也将世界沉管安装的厘米级标准,提升到中国的毫米级标准。
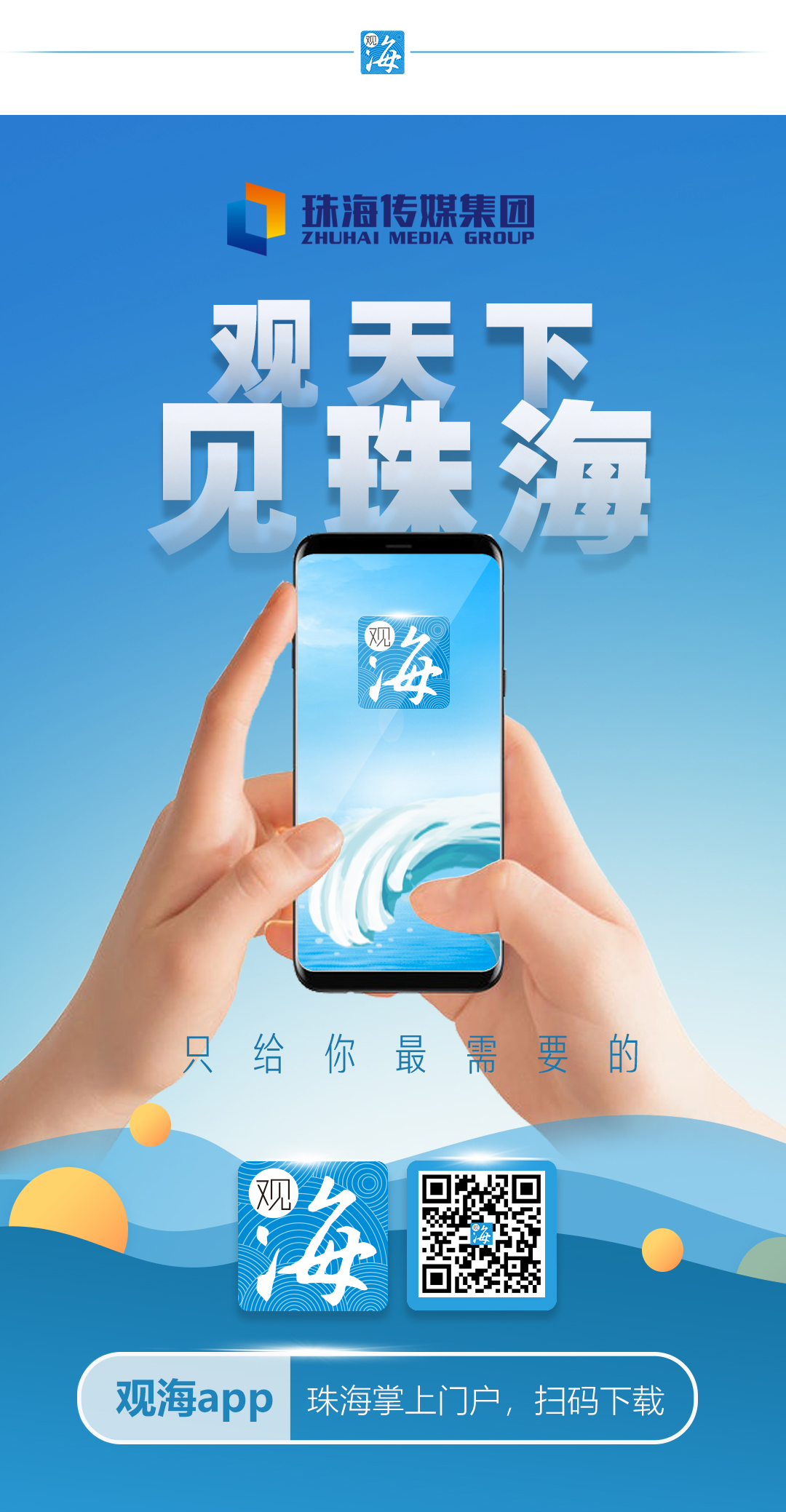
6月11日8时,广东交通集团发布消息,世界最长最宽钢壳混凝土沉管隧道——深中通道海底隧道最终接头顺利推出,贯通测量结果表明,实现了与东侧E24管节精准对接。目前,深中通道海底隧道已实现合龙,将开展最终接头后焊段施工等,力争11月实现隧道贯通;桥梁工程已经合龙,人工岛工程按计划推进,路面、机电、房建交安和管内工程已经全面展开,正向2024年项目建成通车奋力冲刺。
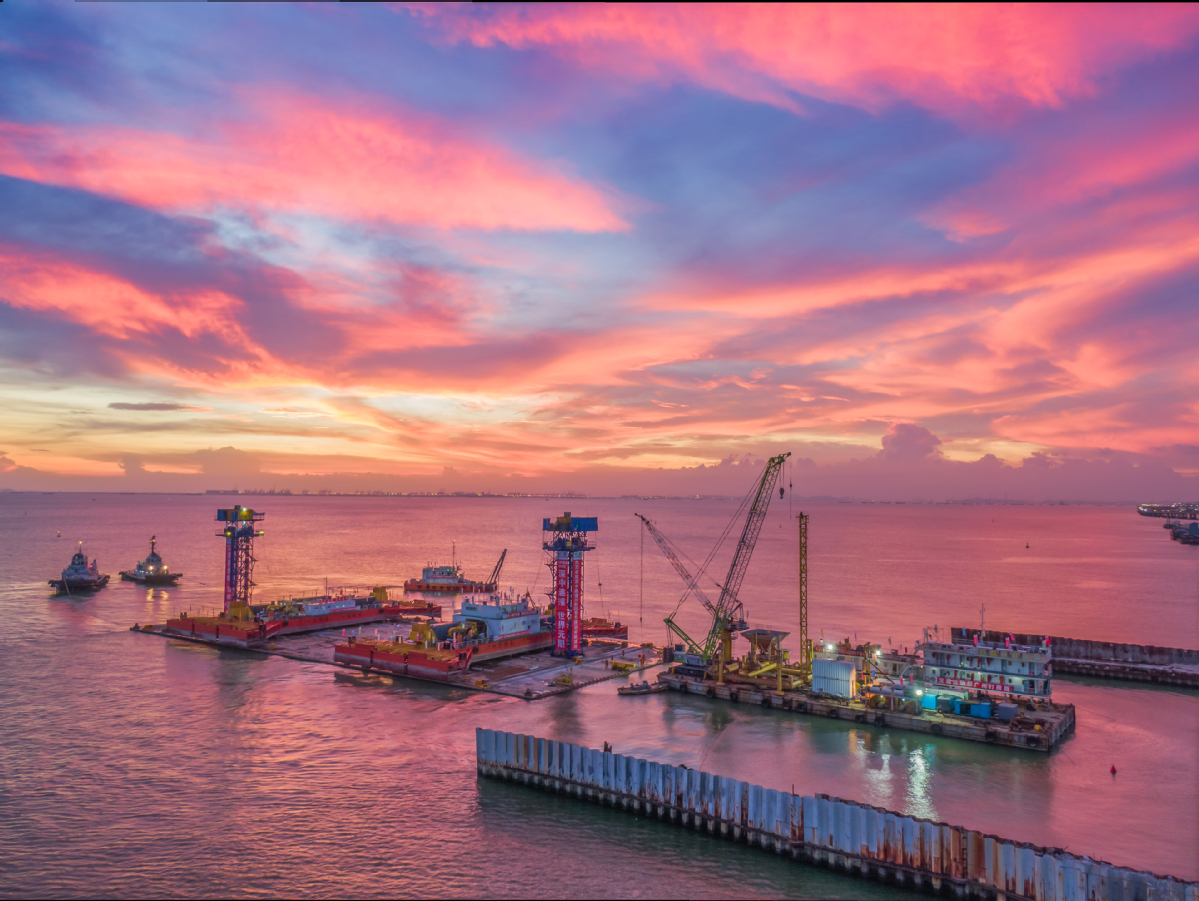
深中通道全长24公里,集“桥、岛、隧、水下互通”于一体。其中,海底隧道长约6.8公里,包含沉管段约5公里,由32个管节及1个最终接头组成。此前,深中通道海底隧道已由东西两侧往中间依次沉放对接了31个管节。6月8日开始最后一个管节(E23)及最终接头的整体浮运安装,至今日完成最终接头推出对接,共用时近70个小时,一举实现关键控制性工程突破。
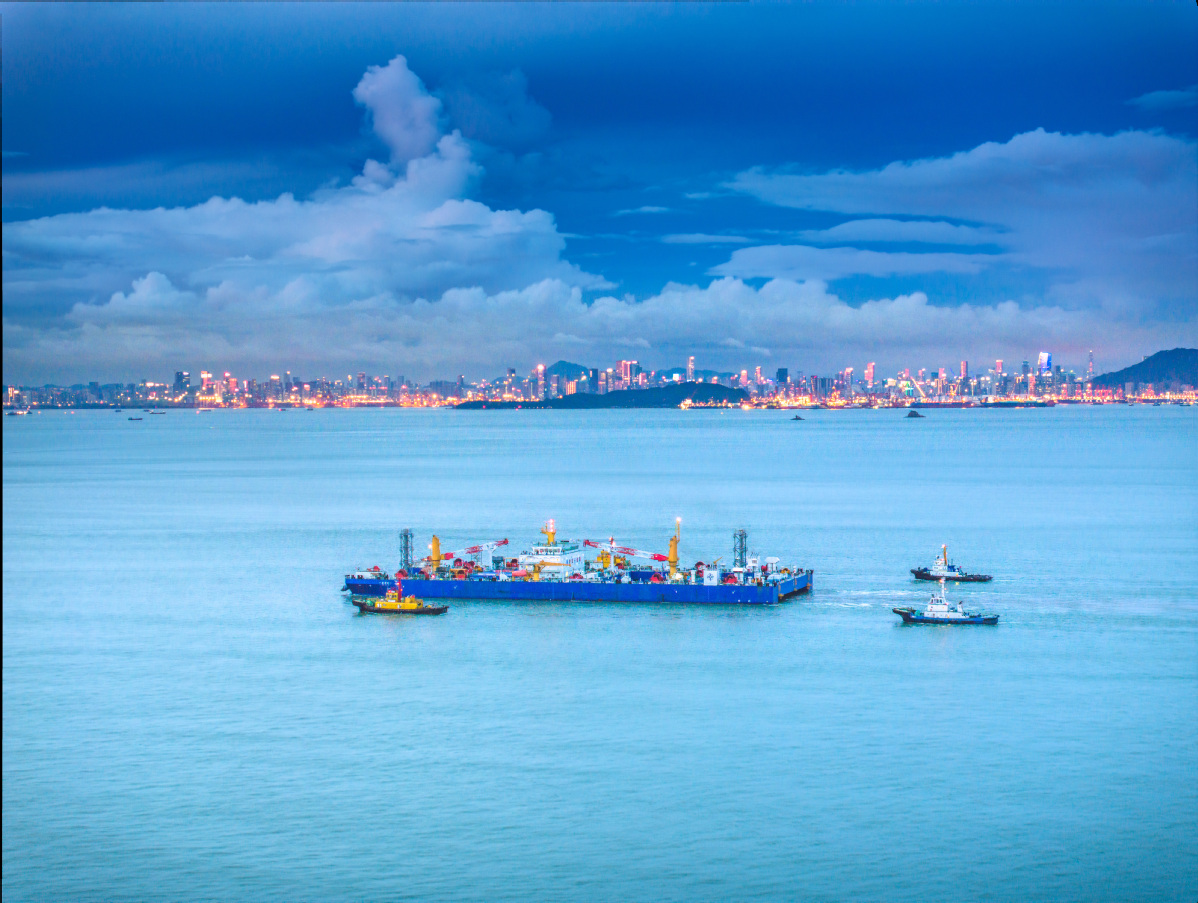
据了解,海底沉管隧道工程共分为三大关键技术:基础处理、管节浮运安装及接头处理。其中,基础处理包括基槽开挖、软基处理及基床整平。基础处理的要求极高,海底20-40米深处基槽开挖精度、碎石整平精度均要求达到亚米级,堪称“海底绣花”。深中通道项目采用的复合地基处理新技术,软土地基沉降控制在48毫米以内,达到国际领先水平。海底隧道长约6.8公里,总用钢量约32万吨。其中一个标准管节长165米、宽46米、高10.6米,立起来就是一幢55层的大楼。平均每节沉管的用钢量约1万吨,焊缝长度超过270公里。
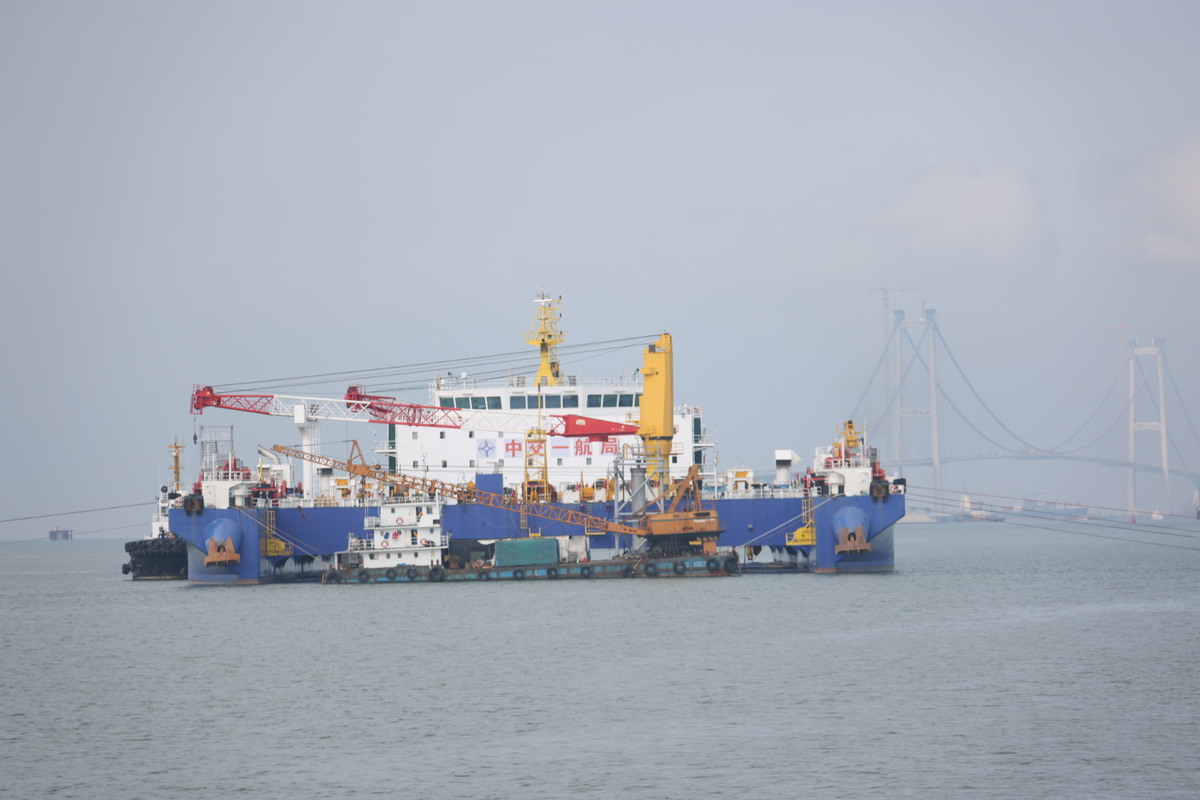
钢壳制造完成后,由中交四航局桂山岛沉管预制厂负责23个管节的预制,保利长大黄埔文冲龙穴岛沉管预制厂负责9个管节的预制,两处均采用智能浇筑系统进行自密实混凝土的浇筑。中交四航局深中通道项目部生产副经理罗兵介绍,经过三年多的平行研究,开展了上百组模型试验,项目研制出了高稳健、高流动性的自密实混凝土,还研发出了具备自动寻孔、自动行走、自动控制浇筑速度的智能浇筑装备及系统,极大提升了浇筑质量和速度。据了解,深中通道钢壳沉管管节共浇筑了近90万立方米的自密实混凝土,检测表明,混凝土填充密实性达到国际领先水平。
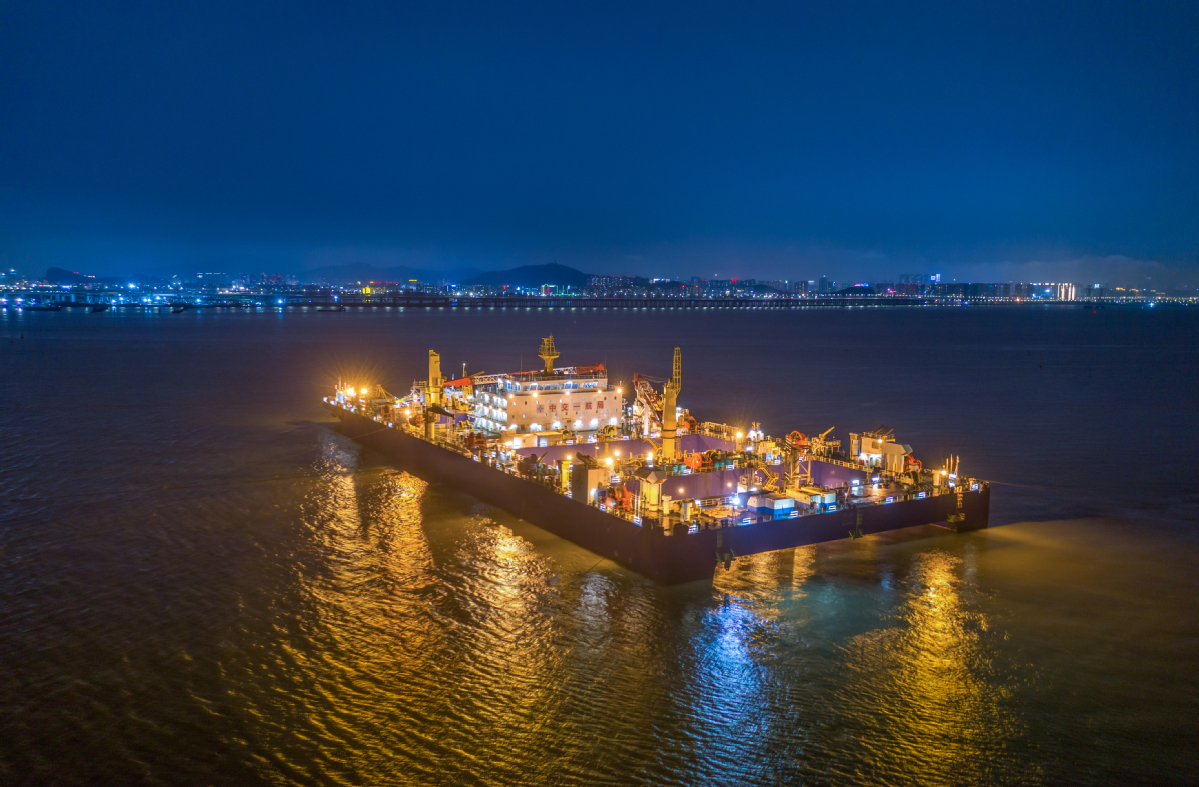
6月11日,深中通道最终接头实现了与E24管节的精准对接。据悉,深中通道沉管隧道采用的整体预制水下管内推出式最终接头,是世界首创的全新结构装置,将最终接头与最后一节沉管(E23)一同制造,推出段放置在管节对接端的扩大端内,与最后一节沉管一并浮运沉放,待最后管节标准段与已安装管节完成对接并确认姿态合适后,推出段就像一个巨型的抽屉内盒,利用千斤顶将推出段(抽屉)从一侧推出,与E24管节的端钢壳完成对接。
深中通道管理中心总工程师宋神友介绍,这种接头具有安全性好、施工快速、不需要大型装备、经济性好等优点。创新采用这种新接头形式的出发点和目的,是希望在外海沉管隧道建造中,形成更加安全、更加高效、更加精准的对接,同时在世界沉管隧道施工领域中实现新的突破,扩大我国在该领域的领先优势。
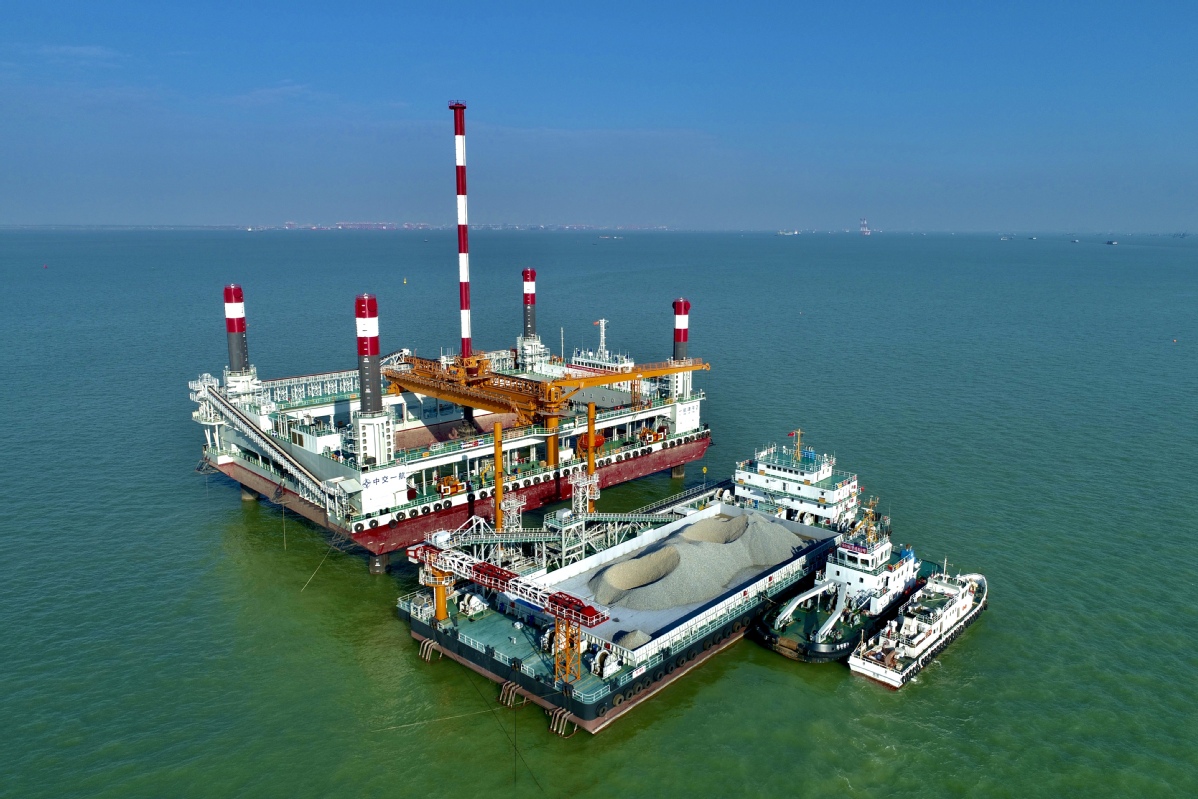
为了实现沉管超长距离的安全浮运,并进一步提升沉管安装的精度,历经三年的平行研究,深中通道建设团队研发了世界首艘且唯一一艘沉管浮运安装一体船“一航津安1”,它是当前世界上安装能力最大、沉放精度最高、施工作业最高效、性能最先进的沉管运输安装专用船舶,可满足8万吨级沉管50公里超长距离安全浮运安装作业,减少伶仃航道占用时间80%以上,减少临时航道挖泥70%以上,沉管浮运安装效率较传统工艺提升一倍以上。沉管浮运安装一体船系统性革新了世界沉管浮运安装工艺,也将世界沉管安装的厘米级标准,提升到中国的毫米级标准。
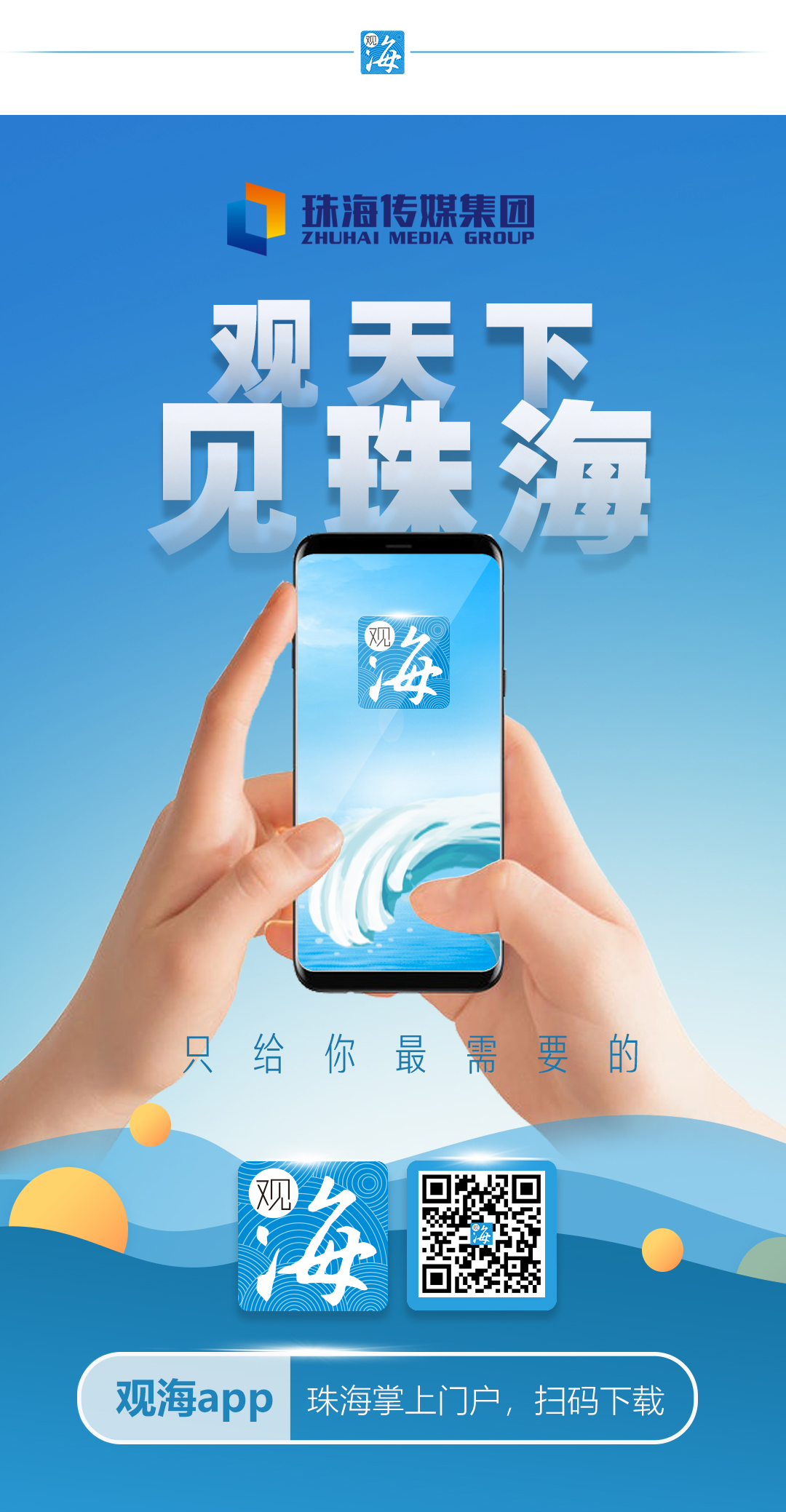
-我已经到底线啦-
暂时没有评论